突發事件襲來,凸顯“零庫存”弊端
隨著現代企業生產朝著機械化和高科技化方向發展,企業的生產管理工作也在逐漸細化。其中一項就是為了降低成本、提高生產效率而出現的壓縮生產原材料庫存的現象。以豐田公司為例,豐田公司名為“看板方式”的生產模式得到了全球企業界的贊賞,即在需要時購進相應的原材料,盡量降低庫存的生產模式。這種模式固然有其可取之處,但當突發事件發生時,這種低庫存的現象就可能影響企業的正常經營。
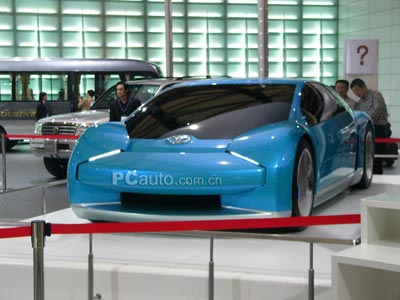
在應對突發事件方面,1995年日本發生阪神大地震和今年上半年“非典”疫情流行期間,日本的一些企業就因原材料供應不及時而大傷腦筋。此后,日本不少企業都采取了原材料供應多元化,分散采購的進貨方式。此次爆炸事件更使日本企業認識到多元采購的重要性。
除自然災害這種無法抗拒的原因外,人為的或潛在的管理漏洞也是導致突發事件發生,影響企業正常經營的一個關鍵因素。據調查,20世紀90年代以后,日本一些企業為了降低成本,出現生產設備更新換代慢和維護簡單化的現象。這一現象的直接結果就是,日本制造業設備的平均年齡由1991年的9.3年上升到去年的12年,這一數字遠遠高于美國平均7.9年的情況。(人民網)
[上一頁] [1][2]


|